Plasma bonding is the utilization of plasma technology to increase a material’s adhesion potential through a process called surface activation. Some materials such as certain plastics and metals do not have very high adhesion capabilities, meaning glues and paint do not adhere to their surface effectively.
Plasma bonding is the process that fixes that problem without compromising the material’s functionality. When an object undergoes a
plasma bonding process, the contaminants on the surface are eradicated and the surface energy is raised. The higher a surface energy an object has the more bonding strength it gains.
The Techniques for Plasma Bonding
Plasma bonding comes in two forms: Atmospheric pressure and low-pressure. Low pressure
plasma bonding uses a vacuum chamber to create a low-pressure environment which allows for plasma generation without having to use extremely high temperatures. This is the most effective method for
plasma bonding but since it operates as a batch system, it can be inefficient for automated manufacturing lines. Atmospheric pressure
plasma bonding does not require a vacuum chamber; instead it ignites plasma around the surface using electric currents. This process is often cheaper and it can be integrated into an automated industrial line.
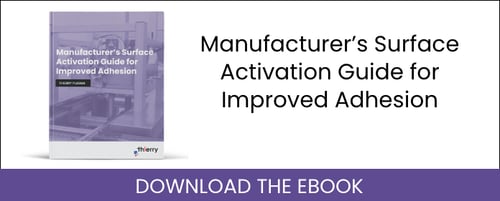