PECVD Is an Improved Method of Chemical Vapor Deposition
Chemical vapor deposition (CVD) is a process in which a gas mixture reacts to form a solid product which is deposited as a coating on the surface of a substrate. The types of coatings that can be obtained by CVD are varied: insulating, semi conductive, conductive, or super conductive coatings; hydrophilic or hydrophobic coatings, ferroelectric or ferromagnetic layers; coatings resistant to heat, wear, corrosion or scratching; photosensitive layers, etc. Different ways have been developed to carry out CVD, which differ by how the reaction is activated. In general, CVD in all its forms achieve very homogeneous surface coatings, especially useful on three-dimensional parts, even with interstices or irregular surfaces difficult to access. However, plasma-enhanced chemical vapor deposition (PECVD) has the additional advantage over thermally activated CVD because it can operate at lower temperatures.
Operation of PECVD Systems
A very efficient way of applying plasma coatings consists of placing the workpieces in the vacuum chamber of a PECVD system where the pressure is reduced to between about 0.1 and 0.5 millibars. A flow of gas is introduced into the chamber to be deposited on the surface and an electric shock is applied to excite the atoms or molecules of the gas mixture. The result is plasma whose components are much more reactive than the normal gaseous state, which allows reactions to occur at lower temperatures (between 100 and 400 °C), increases the deposition rate, and in some cases even increases the efficiency of certain reactions. The process continues in the PECVD system until the coating reaches the desired thickness, and the byproducts of the reaction are extracted to improve the purity of the coating.
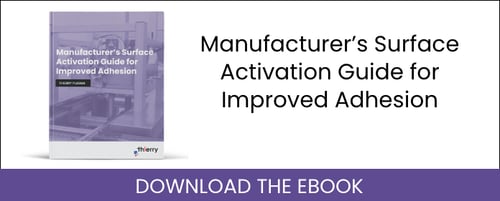